リサイクルサービスRECYCLING SERVICE
長繊維リサイクルカーボンロールの利点と特徴
リサイクル素材のマテリアル化は、再生プラスチックや再生紙などのリサイクル素材を使用して、新たな製品や材料を作り出すプロセスを指します。
◆ 軽量性: 長繊維リサイクルカーボンは非常に軽量です。比重が低く、同等の強度を持つ他の材料よりも軽くなるため、重量の削減や車両の燃費向上などのアプリケーションに適しています。
◆ 高い強度と剛性: 長繊維リサイクルカーボンは非常に強靭であり、高い剛性を持っています。そのため、構造材料や部品の製造において、高い強度が要求される場合に優れた選択肢となります。また、その強度は高温環境でも保持されるため、高温アプリケーションにも適しています。
◆ 耐久性と耐腐食性: 長繊維リサイクルカーボンは耐久性が高く、耐腐食性があります。湿度や化学薬品、紫外線などの外部要因に対して優れた耐性を持っているため、屋外や厳しい環境下での使用に適しています。
◆ 持続可能性: リサイクルカーボンは、廃棄物や副産物から再利用されるため、環境に対する負荷が低い素材です。廃棄物の削減や自然資源の節約に寄与し、持続可能な製品の開発に貢献します。
◆ 設計の自由度: 長繊維リサイクルカーボンは柔軟な素材であり、複雑な形状やデザインに容易に適用することができます。このため、製品の設計の自由度が高まり、創造的なアプローチが可能となります。
◆ 熱伝導性: 長繊維リサイクルカーボンは優れた熱伝導性を持ちます。この特性は、高温環境下での使用や熱制御が重要なアプリケーションにおいて有利です。
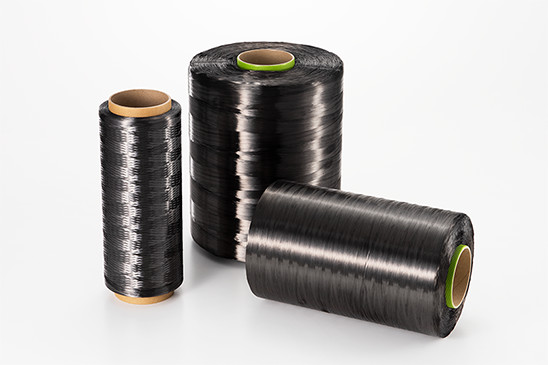
リサイクル素材のマテリアル化
リサイクル素材のマテリアル化は、再生プラスチックや再生紙などのリサイクル素材を使用して、新たな製品や材料を作り出すプロセスを指します。
◆ まず、リサイクル素材のマテリアル化は、収集されたリサイクル可能な廃棄物を適切に分別・仕分けすることから始まります。一般的に、プラスチック、紙、ガラス、金属などの異なる素材が分けられます。
◆ 次に、分別されたリサイクル素材は再加工工程に進みます。この工程では、リサイクル素材が洗浄、破砕、粉砕、溶融、押出し、成形などの過程を経て、新しい形状や形態に変換されます。例えば、プラスチックリサイクルでは、収集されたプラスチック廃棄物が粉砕され、溶かされて再びプラスチックペレットやフレークになります。この再生プラスチックは、新しい製品やパッケージング材料として使用するために再利用されます。
◆ 最後に、再生されたリサイクル素材は、新しい製品や材料の製造に使用されます。再生プラスチックは、容器や包装材、家庭用品、建材など多岐にわたる製品に利用されます。再生紙は、新聞紙、段ボール、包装材、印刷用紙などに再利用されます。再生ガラスは、瓶や容器、建築材料に利用されます。再生金属は、自動車パーツや機械部品などに再利用されることがあります。
◆ リサイクル素材のマテリアル化は、自然資源の消費を減らし、廃棄物の処理量を削減するために重要な役割を果たします。また、リサイクル素材の使用により、二酸化炭素排出量やエネルギー使用量の削減が可能になり、環境への負荷を軽減することができます。さらに、リサイクル素材のマテリアル化は循環型経済を促進し、持続可能な資源管理に貢献する重要な手段となっています。
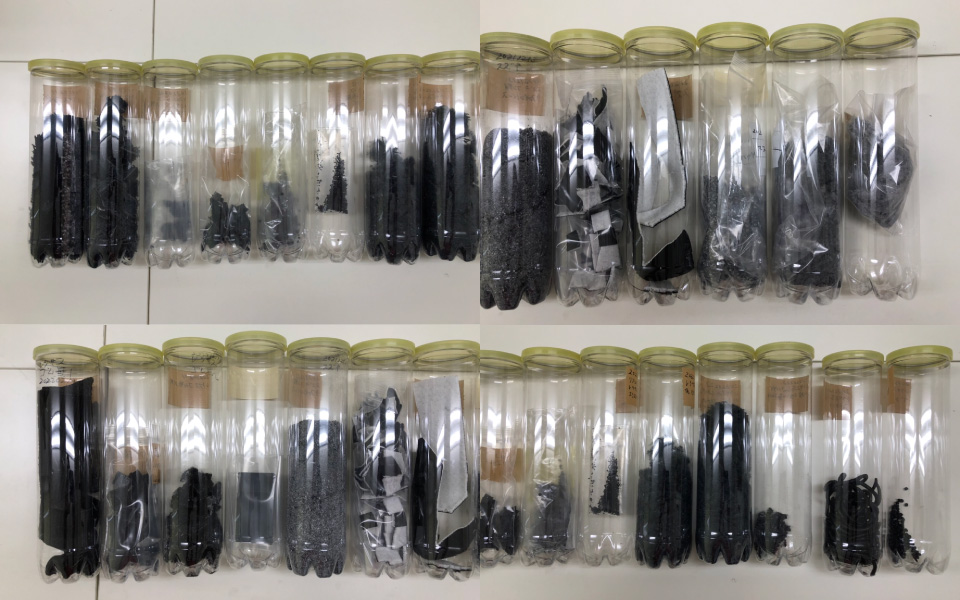
循環型マテリアルリサイクル(Circular Material Recycling)
循環型マテリアルリサイクル(Circular Material Recycling)は、持続可能な資源管理の一環として推進される概念です。従来のリサイクルとは異なり、単に廃棄物を再利用するだけでなく、製品の寿命が終わった後も素材や成分を繰り返し利用することを目指しています。
◆ 収集と分別: 使用済み製品や廃棄物を収集し、適切に分別します。このプロセスは、リサイクル施設や廃棄物管理センターで行われます。
◆ 分解と分別: 収集された製品や廃棄物は、分解や分別されます。部品や素材が取り外され、異なるカテゴリに分類されます。例えば、プラスチック、金属、ガラスなどに分けられます。
◆ 再加工と製造: 分別された素材や部品は、再加工されて新たな製品や材料として使用されます。プラスチックのリサイクルでは、分別されたプラスチックを溶かし、新しい製品に成形することが一般的です。金属やガラスの場合も、溶解や粉砕などの過程を経て再利用されます。
◆ 製品の再利用: 再加工された素材や部品は、新しい製品の製造に使用されます。例えば、リサイクルプラスチックから作られた新しい製品や包装材、再利用された金属から作られた自動車パーツなどです。
◆ 循環型マテリアルリサイクルの目標は、製品のライフサイクルを循環させることで資源の使用を最小限に抑え、廃棄物の発生を減らすことです。このアプローチにより、資源の効率的な利用が促進され、環境への負荷が低減されます。また、廃棄物の処理と排出量の削減にも貢献します。循環型マテリアルリサイクルは、持続可能な社会と経済の実現に向けた重要な取り組みとされています。
エラストマー抽出の流れを右図に示します。
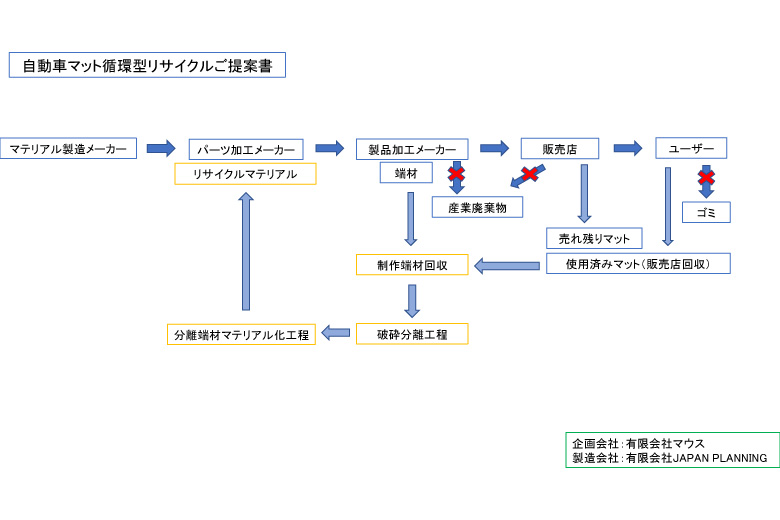
リサイクル自動車マットRPF燃料リサイクル
リサイクル自動車マットRPF(Residue Derived Fuel)燃料リサイクルは、自動車の廃棄物から得られるマットや絶縁材などの素材を再利用し、RPFと呼ばれる燃料に変換するプロセスです。
◆ 通常、自動車の廃棄物処理では、解体された車両から金属部品やプラスチック部品などが回収・リサイクルされます。しかし、リサイクルできない部分の中には、マットや絶縁材といった繊維製品が含まれています。これらの繊維製品は、従来のリサイクルプロセスでは再利用が難しいため、廃棄物として扱われることがあります。
◆ そこで、リサイクル自動車マットRPF燃料リサイクルは、これらの繊維製品をエネルギーとして利用する手法です。以下は、一般的なプロセスの概要です
◆ 収集と分別: 自動車の廃棄物処理施設において、解体された車両からマットや絶縁材などの繊維製品が収集されます。これらの素材は、廃棄物から分別されます。
◆ 副生成物の取り除き: マットや絶縁材などの繊維製品は、他の廃棄物や不純物と混ざっている場合があります。このため、副生成物や不純物を取り除くための前処理が行われます。例えば、繊維を分離するためにシュレッダーや分級機が使用されます。
◆ 乾燥と粉砕: 取り除かれた繊維製品は、乾燥や粉砕の過程を経て、均一な形状となります。これにより、後続の処理が容易になります。
◆ RPF燃料への変換: 乾燥された繊維製品は、RPF燃料として再利用されるために処理されます。RPFは、廃棄物由来の燃料であり、石炭やコークスなどの代替燃料として使用されます。繊維製品は高温処理され、粉砕や圧縮され使用されます。
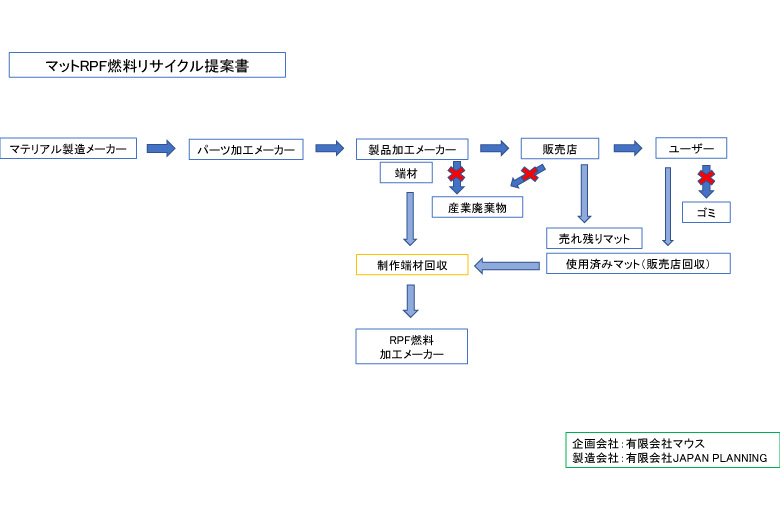
各種マット粉砕分離設備
各種マットの粉砕分離工程は、マット(敷物や絶縁材など)を適切なサイズに破砕し、異なる成分や材料を分離するプロセスを指します。
◆ マットの供給: マットは、適切な供給システムによって粉砕分離装置に供給されます。これには、コンベアベルトやフィーダーなどが使用される場合があります。
◆ 粉砕: マットは、破砕機やシュレッダーなどの機械を使用して粉砕されます。このプロセスにより、マットは小さな断片や繊維に分解されます。粉砕の目的は、マットを均一なサイズにすることであり、後続の分離プロセスを容易にすることです。
◆ 分離: 粉砕されたマットは、異なる成分や材料を分離するために分離装置に送られます。以下に、一般的な分離技術の例を挙げます。
◆ 重力分離: 粉砕されたマットを振動や風力などの力で適切な方向に移動させることにより、異なる密度を持つ成分を分離します。例えば、重い金属や石などがマットから分離されます。
◆ 空気分離: 粉砕されたマットを風や空気の流れによって吹き飛ばすことで、軽い成分(繊維やプラスチックなど)と重い成分(金属やガラスなど)を分離します。
◆ 磁気分離: 粉砕されたマットを磁力の影響を受けることにより、磁性のある金属(鉄など)を分離します。
◆ 光学分離: 光学センサーやカメラを使用して、マットの色や形状などを検知し、異なる成分を分離します。例えば、プラスチックと紙を分離する際に使用されます。
◆ 後処理: 分離された異なる成分や材料は、それぞれの特性に応じて適切な後処理が行われます。
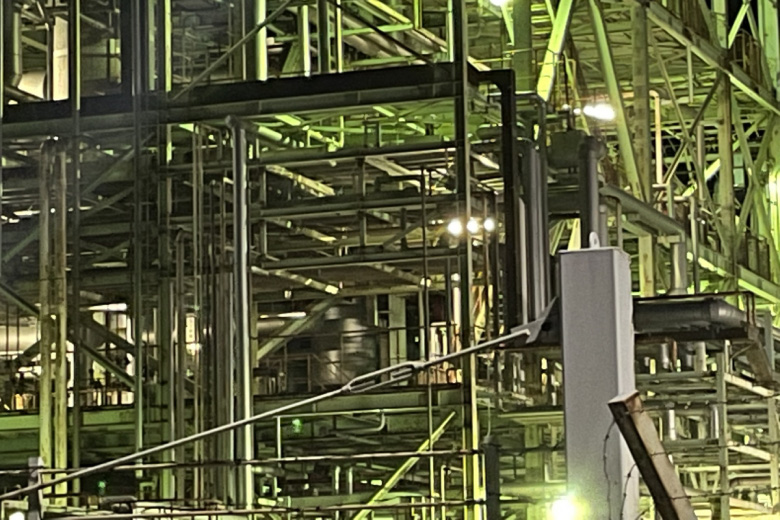
固形燃料ROF製造設備
協力工場によりPP、PET等の廃材から固形燃料RPFの製造を行っています。
◆ 固体燃料ROF(Reduced Oxygen Firing)製造設備は、特定の製造プロセスを使用して固体燃料を生成するための設備です。ROFは、酸素濃度を制御することによって燃焼プロセスを調整し、燃焼反応による煙や有害な排出物を削減することができます。
◆ 燃料供給システム:固体燃料(例:木質ペレット、バイオマスチップなど)を供給するためのシステムです。燃料は適切なサイズと形状に加工され、燃焼プロセスに適した形態になります。
◆ 燃焼室:燃料が燃焼する領域であり、酸素濃度が制御されます。酸素供給が制限された環境で燃焼が行われるため、燃料は不完全燃焼し、煙や有害な排出物の生成が抑制されます。
◆ 酸素制御システム:燃焼室内の酸素濃度を制御するためのシステムです。酸素供給量を調整することで、燃焼速度や燃焼反応を制御し、効率的な燃焼と排出物の低減を実現します。
◆ 排ガス処理システム:燃焼プロセスによって生成される排ガスや廃棄物を処理するためのシステムです。これには、フィルターや除塵装置、ガス洗浄装置などが含まれることがあります。
◆ ROF製造設備は、エネルギー効率の向上と環境への負荷の低減を目的として開発されています。燃焼プロセスの効率化と排出物の削減により、持続可能なエネルギー生産や廃棄物処理に貢献します。
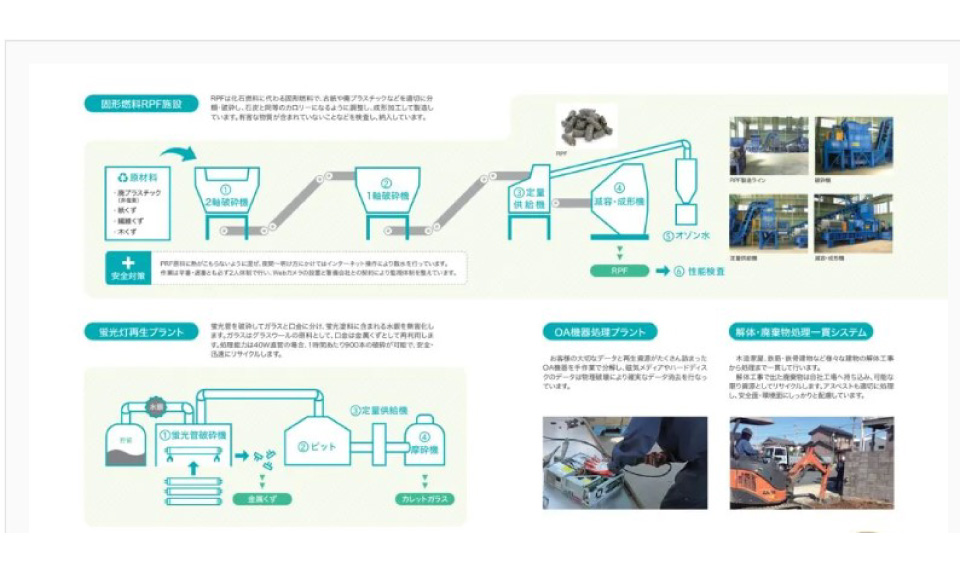
ウォータージェット(ウォーターカッター)加工とは
ウォータージェット加工(またはウォーターカッター加工)は、高圧水流を使用して材料を切削・加工する技術です。
◆ 高圧ポンプ: ウォータージェット加工は、高圧ポンプを使用して水を供給します。通常、ポンプは圧力を上げるために特殊なポンプ(一般的には超高圧ポンプ)が使用され、圧力は一般的に数千から数万ポンドパーキューブインチ(psi)になります。
◆ 混合チャンバー: 高圧ポンプから供給される水は、混合チャンバーに導かれます。混合チャンバーでは、水流に適切な速度と圧力を与えるために、水と空気または研磨材との混合が行われます。
◆ 切削ノズル: 混合チャンバーから出てくる水流は、特殊な切削ノズルを通って放出されます。ノズルの内部形状や口径は、切削される材料の種類や厚さに応じて適切に設計されます。
◆ 材料切削: 高速で噴射される水流によって、材料の切削が行われます。水流は非常に速く、切削力は主に水流の速度と圧力によって生み出されます。水流は、材料上の特定の領域に集中し、その圧力によって材料を削り取ります。
◆ 加工特性: ウォータージェット加工は、さまざまな材料に対して高い精度で切削が可能です。例えば、金属、プラスチック、ガラス、石、木材など、多様な材料を切削することができます。また、ウォータージェット加工は非熱的なプロセスであるため、熱に敏感な材料や熱変質が起こりやすい材料の加工にも適しています。
◆ 切削精度と表面仕上げ: ウォータージェット加工は、高い切削精度と表面仕上げの品質を提供します。
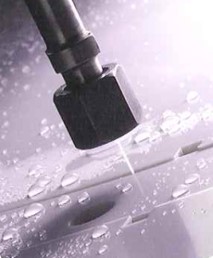
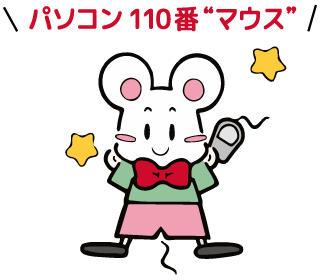